var-Our Story Overview / prop-Our Story Overview
Our Story Overview
var-Sustainability / prop-Sustainability
Sustainability
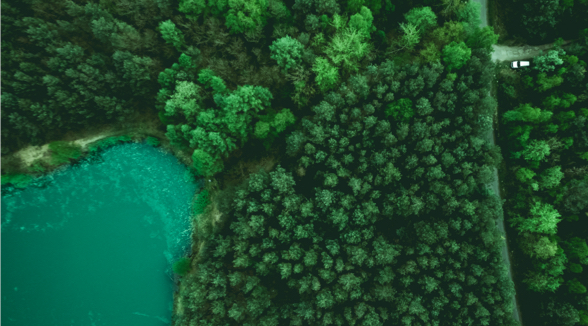
var-Corporate Contacts / prop-Corporate Contacts
Corporate Contacts
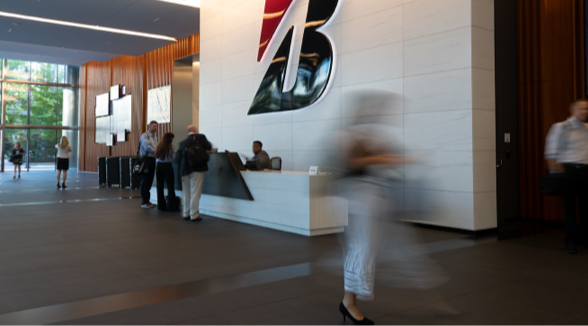
var-Write to Us / prop-Write to Us
Write to Us
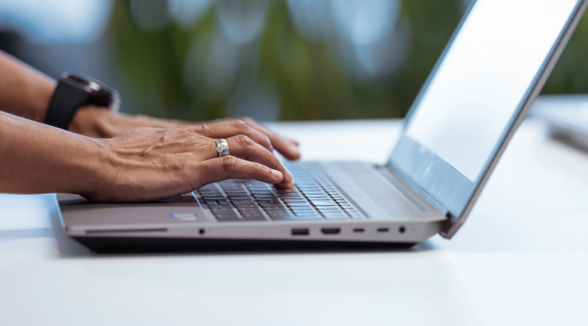
var-Our Locations / prop-Our Locations
Our Locations
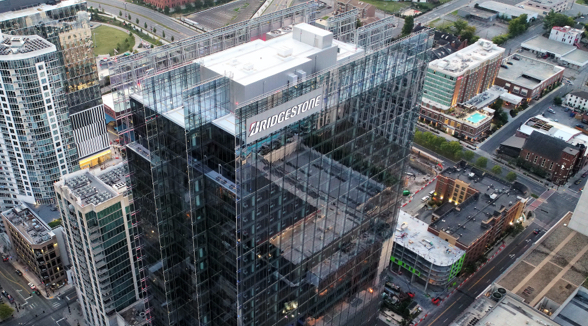
var-Our Headquarters / prop-Our Headquarters
Our Headquarters
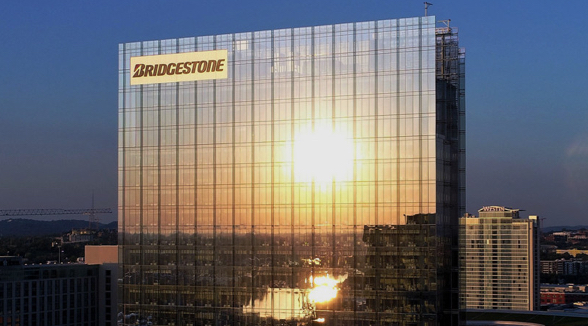